- Mechanical Rooms
- Slabs-On-Deck
- Parking Garages
- Pedestrian Decks
- Locker/Shower Rooms
- 5 gallon white pail - Resin
- 5 gallon black pail - Hardener
- 1 gallon white pail - Resin
- 1 gallon black pail - Hardener
- 50 gallon drum
- Best suited for application in temperatures between 60°F and 90°F.
- FlexPoxy is not designed to be applied as a finish or wear coat.
- It is light-sensitive to ambering over time and requires a UV stable topcoat.
- Personal Protective Equipment (PPE) & clothing per SDS (Safety Data Sheet)
- Jiffy® Mixer Blade (ES Model)
- Clean Mixing Container
- Low Speed/High Torque Power Drill
- Shed-Resistant Roller Cover - 3/8" Nap
- Application Squeegee
- Mix ratio for FlexPoxy is 1 part Resin to 1 part Hardener by volume. 8-16 oz. of ProColor Universal Colorant is recommended per gallon of material. Mix the components thoroughly for 1-2 minutes with a Jiffler ES style mix blade. Mix only enough material at one time that can be applied without exceeding the pot life.
- Concrete must be structurally sound and free of curing membrane, paint, or other sealer. If you suspect that the concrete has been previously sealed, call ProREZ technical support for further instructions.
- Concrete must be dry before application of this floor coating material. Concrete moisture testing must occur. Readings must be below 3lbs/1,000s.f./24hrs (ASTM F1869-11) or 75% internal relative humidity (ASTM F2170-11).
- Avoid scratching or gouging the surface. All floor coatings will scratch if heavy or sharp objects are dragged across the surface.
- Do not drop heavy or pointed items on the floor as this may cause chipping or concrete pop-outs in the case of a weak substrate cap.
- Rubber tires can permanently stain the floor coating from plasticizer migration. Use non-marking tires to prevent discoloration.
- Rubber burns from quick stops and starts can heat the coating to its softening temperature, causing permanent marking.
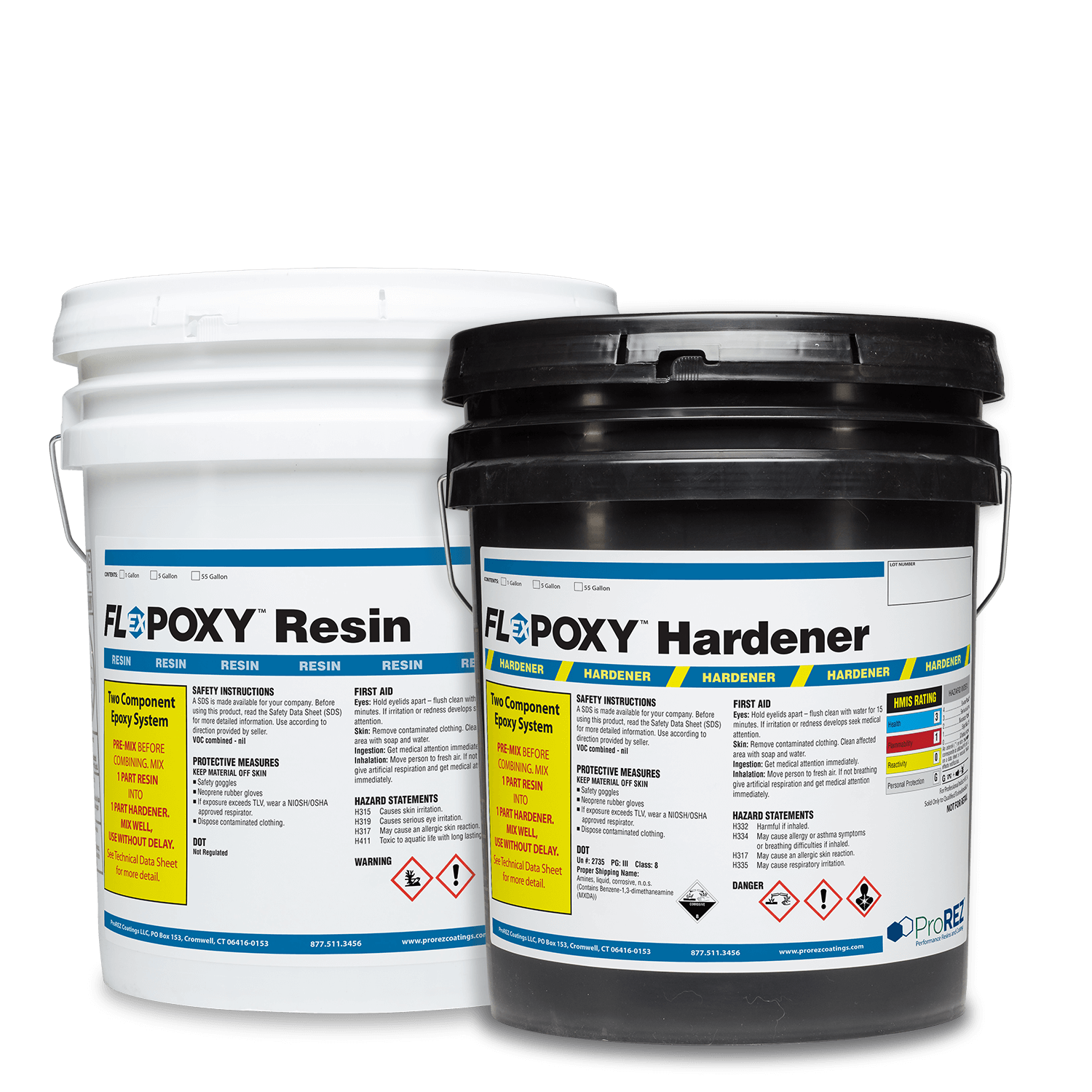
FlexPOXY
FlexPoxy is a uniquely versatile and proprietary hybrid epoxy membrane and coating system. FlexPoxy is a clear two component thermosetting, low odor, 100% solids elastomeric polymer designed for various conditions and substrates. Reference technical data sheet for more information.
Typical Uses
Packaging
Storage
Materials should be stored indoors between 60°F and 90°F.Shelf Life
One (1) year from date of manufacture.Limitations
Products Guide
FlexPoxy Resin | A versatile 1:1 elastomeric hybrid epoxy designed with exceptional built-in resiliency and functionality. With its low viscosity, it can be easily applied when combined with FlexPoxy Hardener. |
FlexPoxy Hardener | Allows for moderate working and cure time when combined with FlexPoxy Resin. |
Mixing Instructions
Preliminary Floor Inspections
Colors
See 'Color Guide'Cleaning Guidelines and Maintenance
Allow floor coating to cure at least one week before cleaning by mechanical means (e.g., sweeper, scrubber, disc machine).Caution
Repairs
Repair gouges, scratches, or chip outs as soon as possible to prevent moisture or chemical contamination.Disposal
Dispose in accordance with federal, state, and local regulations.Physical Characteristics
Hardness (Shore A) | ASTM D-2240 | 80 |
Tear Strength, PIT | ASTM D-1004 | 74 |
Tensile Strength | ASTM D-412 | 1,200 psi |
Tensile Elongation | ASTM D-412 | 200% |
Adhesion to Concrete | ASTM D-4541 | >400 psi, substrate fails |
Impact Resistance | ASTM D-2794 | >160 in/lb |
Water Absorption | ASTM D-570 | <0.1% |
Flame Test | ASTM E-684 | Class 1 |
Kits
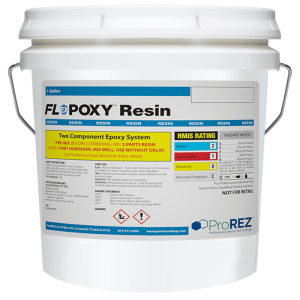
x1
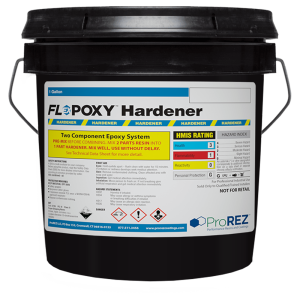
x1
FlexPOXY Kit
FlexPOXY Kit includes
1 FlexPOXY RESIN
1 FlexPOXY HARDENER
Products
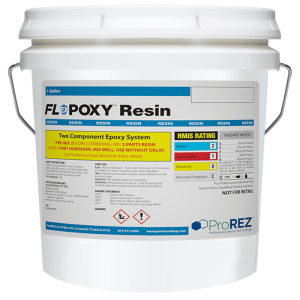
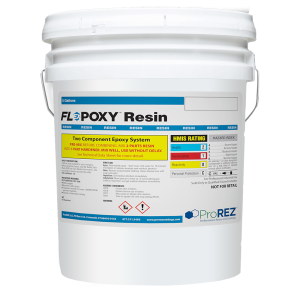
FlexPOXY RESIN
An elastomeric hybrid epoxy resin designed as a waterproofing membrane, joint sealant, and base coat for ProFlex broadcast system. 1 part resin to 1 part hardener. Foot traffic = 14-18 hours.
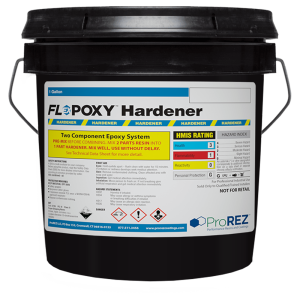
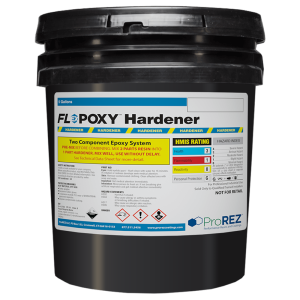
FlexPOXY HARDENER
A low viscosity curative for FlexPoxy Resin. Working time = 30 minutes. Foot traffic = 14-18 hours. 1 part hardener to 1 part resin.